Project Info
Fin tube
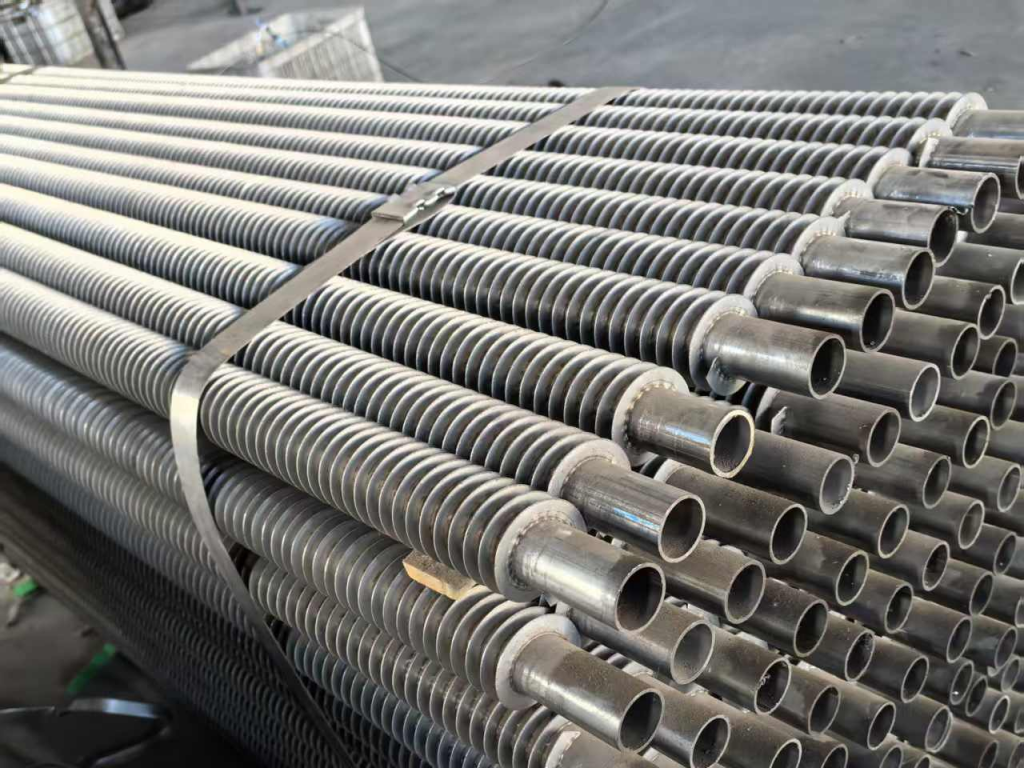

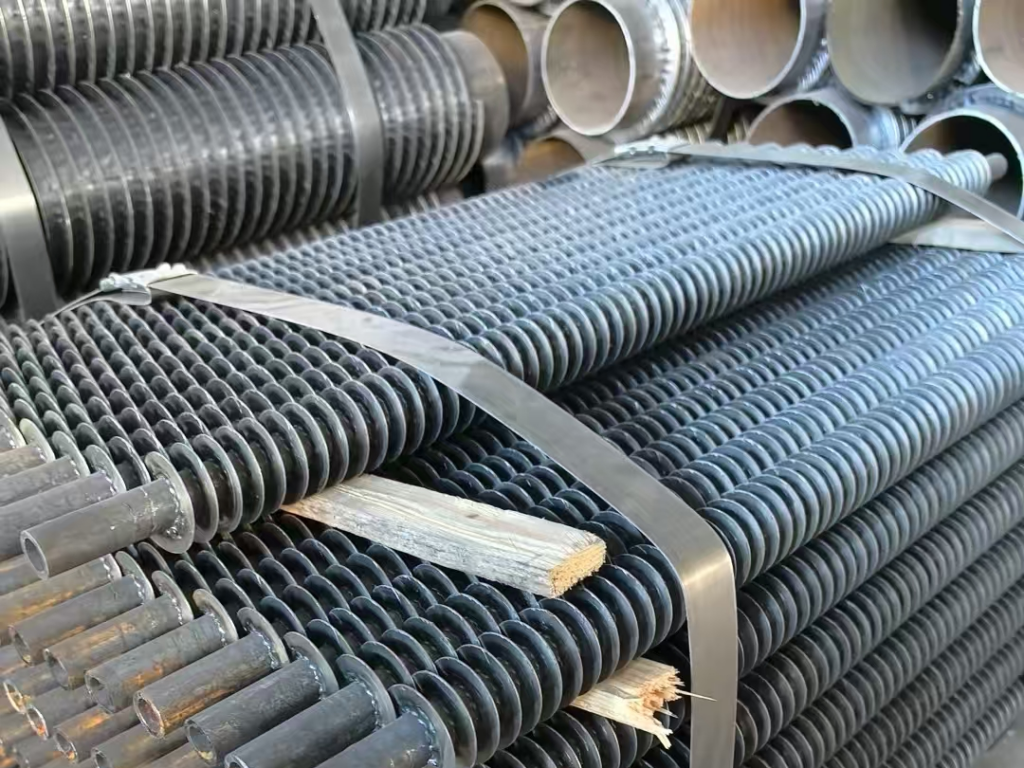
Fin tube is a type of heat exchange element. In order to improve heat transfer efficiency, fins are usually added to the surface of the heat exchange tube to increase the outer surface area (or inner surface area) of the heat exchange tube, thereby achieving the goal of improving heat transfer efficiency. This type of heat exchange tube.
The specifications of finned tubes mainly include parameters such as diameter, length, number of fins, fin height, and fin thickness.
Diameter: There are multiple options for the diameter of finned tubes, including common diameters such as Φ 22, Φ 25, Φ 32, Φ 38, Φ 45, and Φ 50. The diameter of industrial finned tube radiators can be 1 inch (25 millimeters), 1.5 inches (38 millimeters), 2.5 inches (63.5 millimeters), etc., with a maximum of 6 inches (152.4 millimeters). The diameter range of high-frequency welded finned tubes varies from 10mm to 100mm. Smaller tube diameters are mostly used for small precision heat exchange equipment, while larger tube diameters are suitable for large industrial heat exchangers.
Length: The length of finned tubes is usually 1m, 1.2m, 1.5m, 2m, etc., and the specific length can be selected according to actual needs.
Number, height, and thickness of fins: The number of fins affects the heat dissipation area and effectiveness. Common types include 8, 10, 12, 14, 16, etc. The common heights of fins include 1.5mm, 1.8mm, 2mm, 2.5mm, etc. Different heights of fins are suitable for different heat dissipation needs. The thickness of fins is generally 0.12mm, 0.15mm, 0.18mm, 0.2mm, etc., which affects the durability and heat dissipation effect of the radiator. The fin height of high-frequency welded finned tubes is generally between 8mm and 25mm, and the fin spacing is usually between 2mm and 6mm.
2. * * Main features**
-Efficient heat transfer: The fins increase the heat transfer area, significantly improving the heat exchange efficiency.
-* * Compact design * *: Achieve efficient heat transfer in a limited space and save equipment space.
-* * Multiple materials * *: You can choose different materials according to your needs, such as copper, aluminum, stainless steel, etc.
-Corrosion resistance: Some materials and coatings can enhance corrosion resistance and extend service life.
-Widely used: Suitable for multiple industries such as air conditioning, refrigeration, chemical, and power.
3. * * Main types**
-Rolled finned tube: The fins are tightly combined with the base tube through rolling technology, resulting in high heat transfer efficiency.
-* * Wrapped finned tube * *: Wrap the metal strip around the base tube, suitable for high temperature environments.
-Welded finned tube: The fins are fixed to the base tube by welding, and the connection is firm, suitable for high-pressure environments.
-* * Set finned tube * *: Place the fins on the base tube, suitable for low-temperature environments.
4. * * Application Fields**
-* * Air conditioning and refrigeration * *: used for condensers, evaporators, etc.
-Chemical industry: Used for reactors, heaters, etc.
-* * Power industry * *: used for boilers, coolers, etc.
-Oil and natural gas: used for heating furnaces, coolers, etc.
5. * * Selection Guide**
-* * Work environment * *: Choose appropriate materials and types based on temperature, pressure, corrosiveness, etc.
-Heat transfer requirements: Select fin density and height based on heat exchange requirements.
-Space limitations: Choose the appropriate size based on the installation space.
6. * * Maintenance and upkeep**
-* * Regular cleaning * *: prevent dust and dirt from affecting heat transfer efficiency.
-Check corrosion regularly and replace damaged parts in a timely manner.
-Check the connection: Ensure that the fins are firmly connected to the base tube to avoid looseness.
7. * * Frequently Asked Questions**
-Fin detachment: It may be due to poor welding or material issues and requires regular inspection.
-* * Decreased heat transfer efficiency * *: may be due to dust or corrosion, requiring regular cleaning and inspection.
8. * * Summary**
Finned tubes significantly improve heat exchange efficiency by increasing the heat transfer area and are widely used in multiple industries. Choosing suitable finned tubes and maintaining them regularly can ensure their long-term efficient operation.
Application scenarios;
Fin tube radiators are widely used in different scenarios, such as:
Small precision heat exchange equipment: such as the heat dissipation system of electronic instruments, using high-frequency welded finned tubes with smaller diameters to achieve efficient heat transfer.
Large industrial heat exchangers, such as condensers in power plants, use finned tubes with larger diameters to ensure high fluid flow and increase the total heat transfer capacity.
Industrial finned tube radiator: suitable for various industrial scenarios, such as waste heat recovery devices in chemical, metallurgical and other industries.
National standard finned tube radiator: suitable for different environmental usage needs, with different wall thickness specifications, such as over 1.0mm, national standard 1.5mm, and special requirements for wall thickness above 1.5mm.